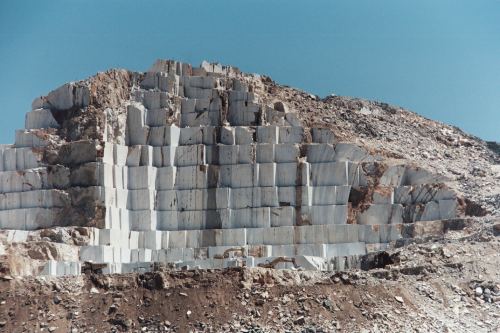
14 Nov El proceso de elaboración del mármol: de la cantera a tu casa
El mármol, una de las piedras naturales más apreciadas en la arquitectura y el diseño de interiores. Sin embargo, antes de que esta piedra pueda embellecer hogares, edificios o espacios públicos, pasa por un riguroso proceso de elaboración. En este artículo te contamos cada una de las etapas de este proceso, desde la extracción en la cantera hasta su instalación final.
1. Extracción en la cantera y transporte
El viaje del mármol comienza en las canteras, donde se extrae la piedra directamente de la tierra. Las canteras de mármol suelen estar ubicadas en zonas montañosas, como las famosas canteras de Carrara en Italia, o en regiones con características geológicas específicas que han permitido la formación de mármol durante millones de años.
Identificación de la calidad y ubicación del mármol
Antes de comenzar la extracción, se realizan estudios geológicos detallados para identificar la calidad y cantidad de mármol disponible en un área determinada. Estos estudios pueden incluir pruebas de perforación para obtener muestras del mármol, análisis de la estructura geológica y evaluaciones de las condiciones de acceso y extracción.
Métodos de extracción
El método de extracción elegido depende de la geología de la cantera, el tipo de mármol y la tecnología disponible, siendo los siguientes los más comunes:
- Corte con hilo diamantado: este método ha revolucionado la extracción de mármol en las últimas décadas. Un cable de acero recubierto con pequeños diamantes industriales corta el mármol con gran precisión, minimizando el desperdicio y reduciendo el riesgo de fisuras en el material. El hilo diamantado se guía a través de la roca, realizando cortes limpios y precisos, lo que permite extraer bloques de mármol de gran tamaño.
- Sierra de cadena: Utilizada principalmente en canteras con mármol de dureza media a alta, la sierra de cadena corta grandes bloques de mármol a partir de la roca madre. Aunque es menos precisa que el hilo diamantado, es eficiente en la extracción de mármol en condiciones difíciles.
- Método de perforación y división: Es una técnica más tradicional que consistí en la perforación de agujeros en el mármol, seguido de la inserción de cuñas metálicas que se expanden para dividir el bloque. Este método es adecuado para mármol con fisuras naturales, donde la piedra se puede separar más fácilmente sin dañarla.
Tamaño y transporte de los bloques
Una vez cortados, los bloques de mármol, que pueden pesar entre 20 y 30 toneladas cada uno, son retirados cuidadosamente de la cantera. Se utilizan grúas y maquinaria pesada para cargar los bloques en camiones de gran capacidad o en trenes especializados. El transporte desde la cantera hasta la planta de procesamiento es una etapa crítica, ya que cualquier daño al bloque puede afectar la calidad del mármol en etapas posteriores.
2. Almacenamiento en la planta
Después de ser transportados, los bloques de mármol llegan a la planta de procesamiento, donde son sometidos a una inspección inicial para evaluar su calidad y determinar el uso más adecuado. Se almacenan en áreas especiales, generalmente al aire libre pero protegidas de condiciones climáticas extremas, hasta que estén listos para ser procesados.
Inspección de calidad
Antes de cortar los bloques, se realiza una inspección visual detallada para identificar cualquier defecto, como fisuras, manchas o irregularidades en el patrón. A veces, se realizan también pruebas adicionales, como la resonancia acústica, para detectar grietas internas no visibles. Los bloques que cumplen con los estándares de calidad se etiquetan y clasifican según su color, patrón y estructura.
3. Corte de los bloques en losas
El siguiente paso en la elaboración del mármol es el corte de los bloques en losas más manejables. Este proceso es crucial, ya que define el tamaño, el grosor y la forma de las losas que se utilizarán en proyectos de construcción y decoración.
Las sierras más utilizadas para el corte de los bloques de mármol son las siguientes:
- Sierras de disco: equipadas con cuchillas de diamante, estas sierras cortan los bloques de mármol en losas de diferentes espesores, generalmente de 2 a 3 cm para uso común en encimeras y revestimientos. La precisión de las sierras de disco permite obtener losas de alta calidad con un acabado suave.
- Sierras de puente: son utilizadas para cortes más precisos y detallados, especialmente en losas que requieren formas irregulares o cortes específicos. Estas sierras permiten ajustar el ángulo y la profundidad del corte, lo que es útil para proyectos personalizados.
- Sierras de banda: utilizadas para cortes múltiples en paralelo, estas máquinas permiten cortar un bloque en varias losas simultáneamente, optimizando el tiempo y la eficiencia.
4. Pulido y acabado: dando brillo y textura al mármol
Una vez cortadas, las losas pasan por el proceso de pulido, una de las etapas más delicadas y cruciales para determinar la apariencia final del mármol.
El pulido se realiza en varias fases, utilizando discos abrasivos de diferentes granos, desde gruesos hasta finos. Este proceso suaviza la superficie de las losas y resalta los colores y las vetas naturales del mármol, en 3 fases:
- Pulido inicial: los discos abrasivos de grano grueso eliminan las irregularidades mayores y comienzan a alisar la superficie. Este paso también corrige pequeños desniveles.
- Pulido intermedio: se utilizan discos de grano más fino para suavizar aún más la superficie. Este paso es fundamental para eliminar cualquier rayadura dejada por los abrasivos más gruesos y preparar la losa para el pulido final.
- Pulido final: Con discos de grano muy fino o utilizando pastas especiales, se da al mármol su brillo característico. Dependiendo del efecto deseado, el pulido puede ser mate o muy brillante. Este último pulido resalta al máximo la belleza natural de la piedra, mostrando la profundidad del color y las vetas.
Acabados Especiales
Además del pulido tradicional, el mármol puede recibir otros tipos de acabados para adaptarse a diferentes aplicaciones y estilos de diseño:
- Acabado envejecido: este acabado da al mármol un aspecto rústico y natural, simulando el desgaste natural del tiempo.
- Acabado flameado: se aplica calor extremo para crear una textura rugosa y antideslizante, ideal para suelos exteriores.
- Acabado satinado: también conocido como “honed”, este acabado es más suave y menos reflectante que el pulido, ofreciendo una apariencia más discreta.
5. Clasificación y selección del mármol
Después del pulido, las losas son clasificadas de nuevo para asegurar que cumplen con los estándares de calidad requeridos. Se evalúan aspectos como el color, la uniformidad del patrón, el brillo y la ausencia de defectos. Este proceso garantiza que solo las losas de mayor calidad se destinen a proyectos de alto nivel.
Dependiendo de las características de cada losa, se seleccionan para diferentes aplicaciones.
6. Corte y diseño personalizado
Después de la clasificación, las losas de mármol pueden ser cortadas y diseñadas según las especificaciones del cliente, con el fin de adaptar las medidas del mármol a las necesidades de cada proyecto. Las técnicas de corte y diseño más utilizadas son las siguientes:
- Corte a medida: utilizando tecnología de control numérico por computadora (CNC), las losas se cortan con precisión milimétrica para adaptarse a cada diseño. Esta tecnología permite realizar cortes complejos y detallados, como curvas, ángulos precisos y patrones decorativos.
- Biseles y bordes: en esta etapa, se añaden detalles como biseles, molduras o bordes decorativos a las piezas de mármol, especialmente en encimeras, mesas o revestimientos de paredes.
- Incrustaciones y mosaicos: para proyectos más elaborados, el mármol puede ser cortado en piezas pequeñas para crear mosaicos o incrustaciones artísticas. Este tipo de trabajo requiere una gran habilidad y precisión, ya que cada pieza debe encajar perfectamente en el diseño.
7. Tratamientos de protección y mejora
Antes de que las losas de mármol estén listas para su instalación, se pueden aplicar tratamientos adicionales para mejorar su durabilidad y estética:
- Aplicación de selladores: Los selladores protegen el mármol contra manchas y derrames, especialmente en superficies expuestas a líquidos, como encimeras de cocina y baños. Estos selladores actúan penetrando en los poros del mármol, creando una barrera protectora sin alterar su apariencia natural. Este tratamiento es esencial para mantener la piedra libre de manchas de aceite, vino, café u otros líquidos que puedan penetrar y causar decoloración. Además, es conveniente aplicar selladores de manera regular para mantener la protección a lo largo del tiempo, especialmente en áreas de alto tráfico o uso intensivo.
- Tratamientos antideslizantes: En áreas donde la seguridad es una preocupación, como en baños o zonas exteriores, se pueden aplicar tratamientos antideslizantes para mejorar la tracción de la superficie del mármol. Estos tratamientos crean una textura sutil en la superficie que reduce el riesgo de resbalones sin comprometer la estética de la piedra.
- Refuerzo con resinas: En casos donde el mármol presenta fisuras naturales o pequeñas imperfecciones, se pueden aplicar resinas transparentes para reforzar la piedra. Este tratamiento no solo mejora la durabilidad del mármol, sino que también puede realzar su brillo y transparencia, proporcionando una apariencia más uniforme y libre de defectos visibles.
8. Empaquetado y transporte final del mármol
Una vez que el mármol ha sido tratado y está listo para su instalación, se procede a la preparación para su transporte. El mármol es un material delicado, por lo que el empaquetado debe ser cuidadoso para evitar cualquier daño durante el transporte.
Métodos de empaquetado
- Cajas de madera: Las losas de mármol se colocan en cajas de madera resistentes, con separadores que evitan que las piezas se toquen entre sí. Además, se utilizan materiales acolchados, como espuma o burbuja, para amortiguar posibles golpes durante el transporte.
- Paletización: Las losas más pequeñas o los mosaicos se pueden paletizar para facilitar su manejo y transporte. Los palets se envuelven con plástico retráctil para mantener las piezas firmemente en su lugar y protegerlas de la humedad y el polvo.
Transporte y Logística
El mármol embalado se transporta a su destino final, utilizando camiones especializados que minimizan las vibraciones y movimientos bruscos, asegurando que las losas lleguen en perfectas condiciones.
9. Instalación del mármol: la fase final
La instalación es la última y quizás la más crítica etapa del proceso de elaboración del mármol. Este paso requiere precisión, experiencia y un alto nivel de habilidad para asegurar que el mármol se coloque correctamente, realzando la belleza del espacio y garantizando la durabilidad a largo plazo.
Para que la instalación sea óptima, el sitio debe estar adecuadamente preparado. Esto incluye asegurar que las superficies estén niveladas, limpias y secas. Cualquier imperfección en la superficie base puede afectar la colocación del mármol y, por lo tanto, debe corregirse antes de proceder.
Métodos de instalación
- Adhesión con mortero o cemento: el método más común para instalar mármol en suelos y paredes es utilizando mortero o cemento. Una capa delgada de mortero se aplica sobre la superficie base, y las losas de mármol se colocan cuidadosamente en su lugar. Es importante que se mantenga una alineación precisa y que las juntas entre las losas sean uniformes.
- Instalación en seco: para fachadas y revestimientos exteriores, a menudo se utiliza la técnica de instalación en seco, donde las losas de mármol se fijan a una estructura de soporte con anclajes metálicos. Este método permite que el mármol se expanda y contraiga con los cambios de temperatura, reduciendo el riesgo de agrietamiento.
Acabado de juntas y sellado
Después de que el mármol ha sido colocado, se rellenan las juntas entre las losas con un material de rejuntado, que puede ser del mismo color que el mármol o un color complementario. Luego, se aplica un sellador adicional sobre las juntas para protegerlas y evitar que se acumulen suciedad o humedad.